We’re taking good care of enterprise first in immediately’s 3D Printing Information Briefs, as Sevaan Group has launched an additive manufacturing service and Farsoon Europe is partnering with MostTech to develop industrial AM to Austria. Transferring on, Additive Industries and Additive Assurance are working collectively to boost LPBF monitoring, and nLIGHT introduced a course of monitoring instrument for the welding market. Lastly, a brand new lab on the College of Texas in Dallas is utilizing 3D printing to effectively produce pediatric listening to help earmolds.
Sevaan Group Expands Manufacturing Providers to Embody AM
Sevaan Group’s Markforged X7 carbon fiber 3D printer produces industrial-grade elements.
Sevaan Group, the father or mother firm of elements contract producer Sevaan Manufacturing, already affords an end-to-end workflow from design, prototyping, and testing to manufacturing, meeting, and ending of manufactured steel elements. Now, to provide its prospects extra decisions and deliverables, the corporate has expanded its manufacturing companies to incorporate 3D printing. Its new AM service contains elements design, prototyping, testing, and manufacturing, in addition to reverse engineering and elements stock auditing to find out parts well-suited for 3D printing. Industrial-grade AM options, comparable to Markforged, are used to create exact parts out of sturdy plastics, steady fibers, and composites. Plus, the corporate can also be 3D printing instruments for its personal in-house wants.
“Our prospects can select to have their required elements manufactured by way of both conventional processes or 3D industrial printing. For sure parts and manufacturing runs, 3D printing can supply particular advantages together with speedy prototyping, a quicker manufacturing turnaround, enhanced high quality and value financial savings, making it a really engaging manufacturing possibility,” mentioned Sevaan Group CEO David Inexperienced.
“Because of AM, prospects who solely require a small variety of elements or maybe longer-lasting parts, now not want to attend for elements to come back in from abroad whereas experiencing downtime, and may discover more cost effective half choices.”
Farsoon Europe and MostTech Announce Distribution Partnership
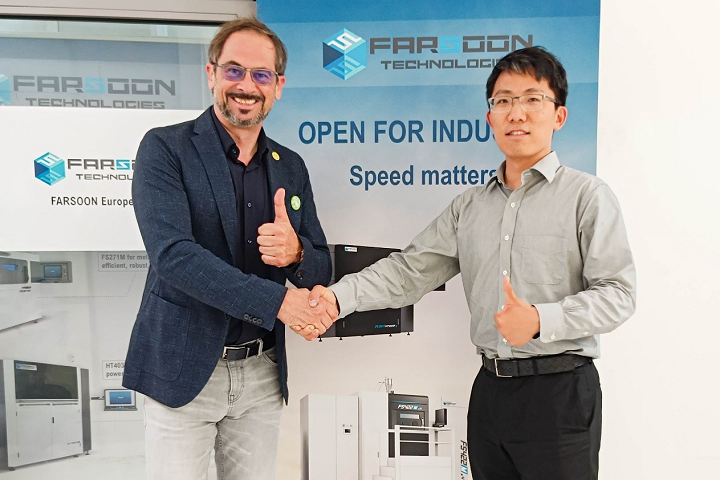
L-R: Michael Hofer, proprietor of MostTech, and Oliver Li, managing director of Farsoon Europe GmbH.
Farsoon Europe GmbH, a subsidiary of Chinese language Farsoon Applied sciences, has established a strategic distribution partnership with Austria-based superior 3D printing options supplier MostTech. The corporate has over three a long time of expertise in supporting industrial prospects by way of expertise consulting, digital administration, 3D printing, and post-processing, and has set itself up as a revered, skilled quantity reseller, particularly with steel AM. Farsoon is a globally numerous firm, and was based with the imaginative and prescient to create open platform methods, in order that customers have freedom to innovate. The partnership between MostTech and Farsoon Europe will enhance technical capabilities in open steel and plastic 3D printing options to serve the wants of native prospects and industries in Austria. MostTech shall be providing Farsoon’s industrial-grade steel and plastic AM applied sciences, supplies, machines, and half manufacturing companies to the Central European market.
“We have now been deeply related to the subject of “Superior Manufacturing” by way of a long time of expertise, from growth to the completed half. Our strategy of “Connecting Folks and Applied sciences” is the assure for sustainable expertise implementations,” mentioned Michael Hofer, the proprietor of MostTech and ManofManufacturing. “The partnership with Farsoon permits us and our prospects to succeed in the subsequent degree of development with industrial additive manufacturing. We’re proud to raise our service portfolio to the subsequent degree with Farsoon.”
Additive Industries & Additive Assurance Enhancing LPBF Monitoring
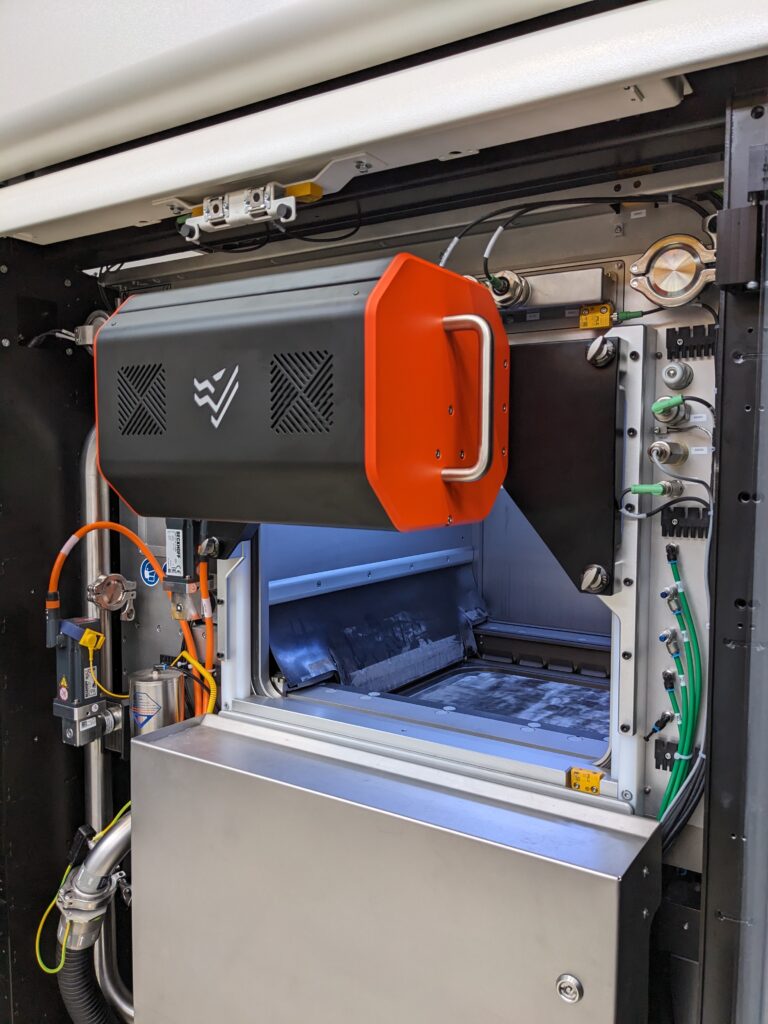
AMiRIS mounted on MetalFAB G2
Additive Industries and Additive Assurance are collaborating to boost in-situ course of monitoring with the previous’s portfolio of MetalFab laser powder mattress fusion (LPBF) printers. These methods have excessive automation, functionality, and scalability, and the brand new MetalFab 300 Flex is claimed to be the one steel 3D printer available on the market with a novel on-demand platform measurement for improved accessibility. AMiRIS by Additive Assurance affords high quality inspection throughout the 3D printing course of, which hastens validation and may end up in larger yield and manufacturing consistency of LPBF elements. As construct charges and productiveness of 3D printers improve, the necessity for in-process monitoring and high quality assurance is larger than ever, and AMiRIS is a logical selection for addressing QA within the MetalFab printers with real-time, in-situ monitoring. The partnership between these two corporations will leverage strengths from each to enhance course of monitoring of high-performance 3D printed elements, and can hopefully lead to broader adoption of LPBF.
“Our partnership with Additive Assurance aligns completely with our dedication to advancing the capabilities of steel additive manufacturing,” mentioned Mark Massey, CEO at Additive Industries. “By integrating AMiRIS® with our MetalFab portfolio, together with our new MetalFab 300 Flex, we’re enhancing real-time high quality assurance, providing our prospects better flexibility, and setting new requirements in manufacturing consistency and reliability.”
nLIGHT’s ProcessGUARD Plasmo Course of Monitoring Methods
Talking of course of monitoring, Vancouver, Washington-based nLIGHT develops, designs, and produces laser expertise merchandise, and puzzled if it was attainable for lasers to finish course of monitoring. Vienna-based plasmo has lengthy been an trade chief in QA and course of monitoring options, and joined with nLIGHT this yr to develop into nLIGHT plasmo GmbH. Leveraging the talents of each corporations, ProcessGUARD was created for the welding market. This course of monitoring resolution places plasmo’s intelligence, energy, and highly effective QA inside an nLIGHT laser. Thus, it’s capable of remove the upkeep and integration complexity inherent in third-party course of monitoring options.
“A very new resolution has emerged from the synergy of our laser and monitoring expertise. Our ProcessGuard affords every part that trendy welding functions want.”
New UT Dallas Lab Makes use of 3D Printing to Produce Listening to Help Earmolds

Earmolds produced within the Callier Medical Innovation Lab.
Not too long ago, the Callier Middle for Communication Problems at The College of Texas at Dallas celebrated the opening of a brand new medical innovation lab, in addition to its use of 3D printing to effectively produce customized earmolds for pediatric listening to aids. Earmolds channel sound from listening to aids to the eardrum, and should be made to suit every affected person’s ear canal; plus, younger youngsters will usually want many units of earmolds of their first 5 years. Conventional strategies of ordering these customized earmolds usually takes two to a few weeks, however through the use of 3D printing, the manufacturing course of is now lower than six hours. Callier Middle leaders are sharing this innovation with different clinics and audiologists across the nation so that every one sufferers can profit from the method. Plus, the middle just lately hosted what it referred to as “a first-of-its-kind” workshop, welcoming over 20 attendees from six states to the brand new innovation lab for coaching in logistics, otoscopy choices, impression scanning, design, 3D printing, and post-processing of customized pediatric listening to help earmolds.
“Callier is dedicated to elevating the usual of affected person care by way of designing revolutionary options to enhance well being care efficacy and effectivity. With the assistance of beneficiant donors, the newly opened Callier Medical Innovation Lab is altering how earmolds for listening to gadgets are produced, offering coaching workshops for audiologists and clinics, collaborating with different departments at UT Dallas, and a lot extra,” Angela Shoup BS’89, MS’92, PhD’94, the Ludwig A. Michael, MD Callier Middle Government Director, mentioned on the ribbon-cutting. “That is one instance of the kind of medical innovation made attainable by way of neighborhood help of the medical innovation lab.”
Subscribe to Our E mail E-newsletter
Keep up-to-date on all the newest information from the 3D printing trade and obtain data and affords from third occasion distributors.